Words by Lidia Ratoi
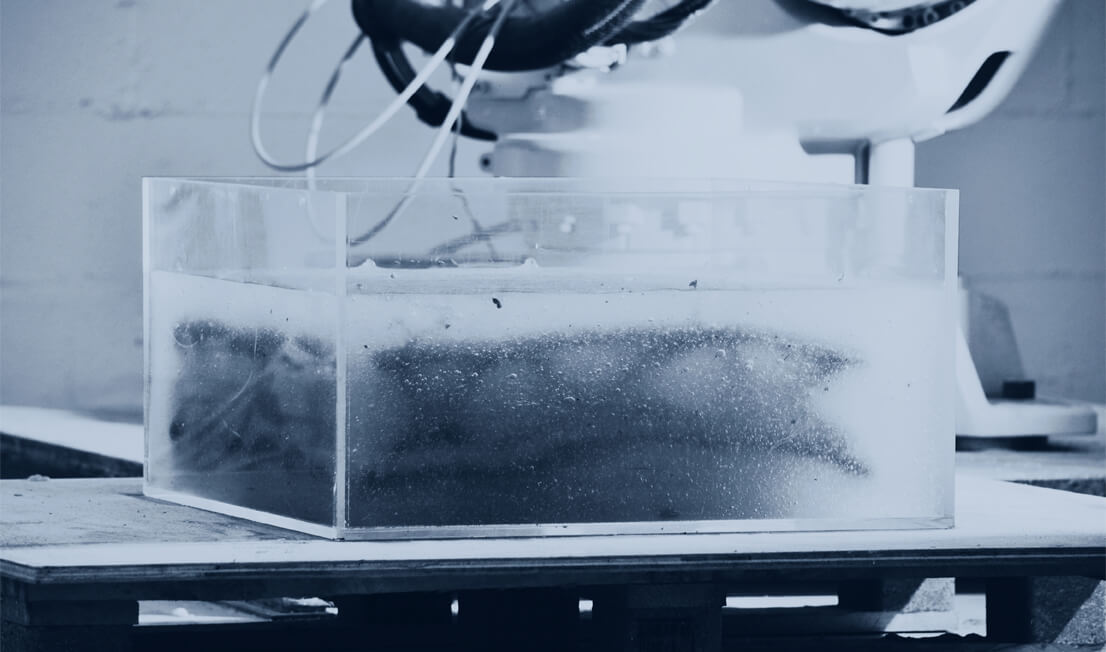
3D Printing is an increasingly popular fabrication technique – we are witnessing many materials, from plastic to bio-resin, machines such as small 3D printers or large-scale robots, or geometrical choices. But the field is far from becoming obsolete – it’s constantly renewing.
During a workshop led at the National School of Architecture Paris-Malaquais, the team consisting of Amaury Thomas and Jim Rhone faced the challenge of producing multiple non-standard 3D constructive nodes for a lightweight and intricate structure. For that time, they used a “combination of foam robotic milling and resin injection moulding. Though reaching interesting results, the method was time and material consuming as each cast was used for a single node only”.
Wanting to fabricate faster and with lesser formal constraints, they came up with the idea of reusable and adaptable casting and discovered that scientists operating in the medical field were experimenting with “a process that would allow them to 3D print soft microscale tissues in gel suspension with thin needles. The main interest was that it opened new possibilities for reproducing complex organic structures or systems that had never been synthesized before”.
They decided to adopt a similar technology for the Design and AEC industries on a larger scale. A few months later, at the Sensitive Robotics workshop, within Design Modelling Symposium Paris 2017, they were 3D printing sealing resin “to experiment new morphologies and rapid prototyping”, thus giving born to the Soliquid project.
Amaury Thomas and Jim Rhone consider that their technique is not better but complementary to traditional additive manufacturing, stating that “it provides totally new ways to consider large scale 3D printing and brings solutions to many limitations inherent in the existing additive manufacturing processes”. From a sustainable point of view, it is a technique that creates no waste since there is no support material. From an artistic and architectural point of view, this technique offers a generous palette of formal language.
Limiting the gravity-related effects that constrain basic additive manufacturing to bottom-up and layer-by-layer printing, it is basically as if you were drawing in the 3D space with an instant curing material, ” additionally an incredibly fast printing approach.
The technology holds the potential to become the new, established means of 3D printing. Frequently asked questions or doubts about Soliquid technology are mostly related to scalability aspects and materials we can use, the team narrates. However, as far as dimensions are concerned, our technology is entirely scalable, and we are working on improvements to be able to 3D print in large tanks anytime soon. Massive tanks could produce elements of any size, even non-standard prefabricated and modular structural systems for large-scale construction applications.
Amaury Thomas and Jim Rhone are very enthusiastic about the future of 3D printing generally, stating that the coming year will be very interesting when it comes to material innovation and hybridisation—and looking at how a new machine can entirely change the formal alphabet we have been accustomed to.