Interivew by Sebastian Kamau

Suzanne Lee needs little introduction as a pioneer in the fabrication of consumer materials from biomedia. Since the early aughts, Lee has carved herself a niche between the fields of fashion and biology that combine elements of inventiveness, sustainability, and a genuine passion for shaping a more resilient world. As the Chief Creative Officer at Modern Meadow, the founder of the BIOFABRICATE conference, and the former director of the design consultancy BioCouture, she stands as a living nexus of the interface of design and biology.
Lee’s career in the arts began with degrees in Fashion Design from the Central Saint Martins College of Art & Design and in Digital Arts from Middlesex University. Both between formal schooling and after, Lee worked with brands like Hussein Chalayan, Puma and Jenny Packham to develop a practical understanding of how the fashion industry sources and develops products.
Her deeply researched 2005 book, Fashioning The Future: Tomorrow’s Wardrobe, grew out of her experiences as a Senior Research Fellow at Central St. Martin’s and delves deep into the role of emerging technology in an imagining of a ‘future wardrobe.’’
Her introduction to the world of biofabrication came serendipitously at an art gallery in 2002 where she met David Hepworth, a materials scientist. They worked together on a fashion project using the ‘Symbiotic Culture Of Bacteria and Yeast’ (SCOBY) traditionally used to make kombucha as the foundational material for a line of speculative biker jackets, bombers, and quasi-denim jackets.
The project garnered a great deal of press which, in time, led her to become a 2011 TED fellow and form her own biological design consultancy, BioCouture. Her work at BioCouture drew the attention of Andras Forgacs, CEO of the biomaterials start-up Modern Meadow, who tapped her to lead the creative effort for their leather initiative.
Since joining in 2014, Modern Meadow has launched the world’s first bioleather materials brand – Zoa™. A graphic tee made from Zoa™ was shown at the Museum of Modern Art fall 2017 exhibition, Items: Is fashion Modern?
Suzanne Lee has broadened the potential for applying biological materials in the fabrication of consumer goods. As the field continues to grow, we look forward to seeing the shapes it will take next.
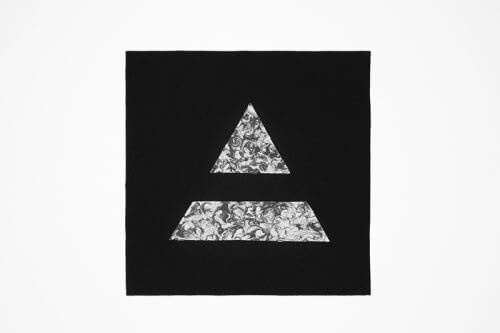

Considering programmable matter to growing materials, advancements in material development are at a turning point. What do you think are the key drivers that will shape the future of biomaterials in the not-too-distant future?
The biggest driver of material innovation in recent years has been sustainability and the search for materials with lower environmental impact. Animal agriculture in particular has an immense environmental impact on land, water, food, and energy. A secondary driver is brands seeking to optimize and simplify supply chains, reduce costs and find new manufacturing efficiencies. Then, finally, I would say is a creative imperative to seek the new and reinvent constantly.
What are the biggest challenges facing the development of biomaterials?
With such long-established raw material supply chains whether from agriculture, livestock or oil, it’s always challenging for new materials to compete on price. Commodity fibres are the most challenging of all, and that’s why you see the majority of smart biofabricated material startups going after the highest-value density materials like silk and leather. In addition to competing on price, biofabricated materials need to at least meet the same material properties in terms of technical specification as well as aesthetics: does it look, feel and perform as well as, if not better than, a current product?
Biotechnology is facilitating a new material revolution; both bio-based and environmental friendliness materials are becoming increasingly important. What are for you the most exciting materials and material combinations?
For me the most exciting materials are the ones that will succeed in doing both the above: being better for the planet and for the customer! We’re seeing multiple companies tackle leather in new and interesting ways, with various technology approaches including tissue engineering (using mammalian cells), fermentation (using yeast cells) and filamentous fungi (using mycelium). Each of these materials yields different properties and it’s early days to see which technologies will succeed in the marketplace. Biofabricated materials have the potential to offer new functionalities to the customer – they can be more lightweight, combine different materials together in novel composites, and offer new design possibilities. In the case of biofabricated leather materials, they can deliver efficiencies to manufacturers in terms of being a regular size and shape with none of the classic challenges of traditional leather, such as insect bites, scars, etc.
I’m excited by spider silk materials and their potential to be blended with other fibres to bring new functionality such as strength and warmth whilst being lightweight. I’m also a huge fan of companies like Biomason which are growing building materials like bricks and tiles in greenhouses. Instead of shipping these heavy materials around the globe, they can be grown locally, using grey water and local aggregates producing materials that are even stronger than current products and with a massively improved environmental footprint.
At the end of this year’s BIOFABRICATE conference, the Parley x BIOFABRICATE collaboration was announced. A project between BIOFABRICATE and Parley for the Oceans to create a “future island”, an island where nothing is made of virgin plastic. For those that could not attend this year’s edition could you tell us a little bit more about it?
At Biofabricate we have been fans of Parley for the Oceans for a number of years now. Parley has succeeded in bringing awareness of the calamitous situation we have created with ocean plastic, not by admonishing people for irresponsible behaviour, but by seeking to work constructively with brands such as Adidas to tackle the problem head-on. Parley is both an advocate for the oceans and for changing the materials we use in all our consumer products. They’ve shown how it’s possible to turn trash into gold. In 2018 Adidas is forecast to be selling millions of pairs of shoes using recycled ocean plastic instead of virgin plastics from oil.
That’s just the beginning. The next step for Parley is championing new biobased materials for a post-plastic world. We can’t think of a better laboratory than our pristine ‘Future Island’ in paradise, where we want to see if it’s possible to create an environment that’s entirely plastic-free. So we’re working together to come up with material solutions that work in harmony with the planet. We see bio-fabricated materials as new solutions in that effort.
What direction do you envision taking Biofabricate Conference into?
Our partnership with Parley is obviously a deep and long-term commitment. We’ll be working on initiatives that collectively foster and support material eco-innovation. We’re also looking into ways to bring Biofabricate to new locations globally, maybe initially in TEDx style. There are so many burgeoning local communities around the world innovating with biofabricated materials, especially in Europe. I’d love to bring Biofabricate to those audiences and share their great work more widely.
Biofabricate has become THE global event for sharing the latest innovation in Biofabricated materials. We were proud to work with Adidas to launch their Futurecraft Biofabric shoe in 2016 and with Biomason to launch their Biocement bricks. We’re looking forward to further biofabricated material launches in 2018!
What is your chief enemy of creativity?
You mean what stops me from being creative? Lack of sleep?
You couldn’t live without…
The amazing Biofabricate team includes Amy Congdon, Ben Kellogg and team, Cas Smith, Ali Schatschneider and Emma van der Leest who work crazily hard to put on an amazing event each year. I couldn’t do it without them.